- Un importante azienda produttrice di sensori, per realizzare il cavo di alimentazione di un sensore cilindrico, stampava un gommino plastico, lo applicava ad un cavo incollandolo ed assemblava il tutto dentro ad un foro circolare di un bicchierino plastico per poi resinare il sistema al fine di garantire una tenuta IP65.La normativa di questo sensore inoltre prevede che il cavo del sensore resista ad una trazione di 8 kg senza sfilarsi.Quando questo cablaggio è stato chiesto a BREDI abbiamo cercato una soluzione per costampare il passacavo direttamente sul cavo.Il giusto compromesso tra forma/dimensioni e durezza del costampaggio ha generato una soluzione che ha consentito al cliente di accorciare il processo produttivo, diminuire gli scarti di produzione e ridurre il numero di fornitori migliorando quindi il proprio sensore riducendone i costi produttivi.Era l'anno 2007 quando iniziammo a lavorare su questo progetto fornendo i primi campioni e 10 anni dopo continuiamo a fornire il cablaggio di quel sensore.
- Cliente 2 Noto produttore di macchine per la gestione del contante cercava un punto di svolta progettandosi e realizzando il proprio sensore di riconoscimento delle banconote, "cuore" delle proprie apparecchiature.Spazi miniaturizzati e segnali ad alta frequenza erano le maggiori criticità per interconnettere tutte le schede del sensore.Inizialmente coinvolta per quotare dei cavi FFC Bredi ha proposto un kit di cavi pre-assemblati e schermati aumentando l'efficienza del sensore e semplificandone l'assemblaggio.Negli anni l'azienda ha aumentato notevolmente le proprie vendite e quando progetta nuovi sensoricontinua a coinvolgere Bredi per interconnettere le proprie schede.
Case History
Un importante azienda produttrice di sensori, per realizzare il cavo di alimentazione di un sensore cilindrico, stampava un gommino plastico, lo applicava ad un cavo incollandolo ed assemblava il tutto
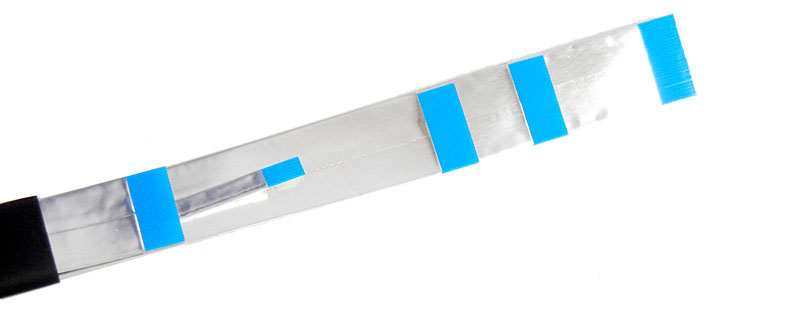